Sep 7, 2023 - 3-5 minutes
What You Need to Know to Make the Switch to UV Acrylic PSAs
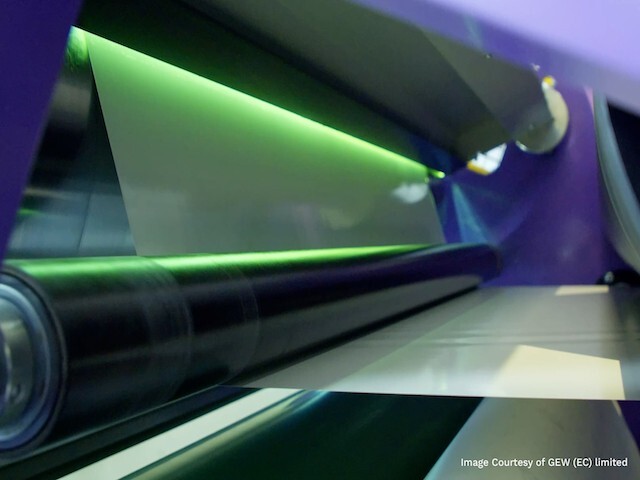
Learn how UV acrylic PSAs offer 100% solids, high durability, fast curing, and more, without the drawbacks of solvent acrylic and hot melt PSAs. Explore the benefits, equipment transition, and expert support with Bostik for a seamless switch to UV acrylic PSAs.
As a converter using pressure sensitive adhesives (PSAs), you may be looking for ways to reduce or eliminate solvents to decrease environmental impact and safety concerns without impacting performance or processing speeds. However:
- If using solvent acrylic PSAs, you may be worried that you won’t find a more sustainable solution that still offers the same superior durability performance.
- If using rubber-based hot melt PSAs, you may be concerned that an alternative won’t offer fast processing.
Fortunately, UV acrylic PSAs provide a more sustainable alternative without impacting performance or processing, offering:
- 100% solids to eliminate solvents
- High durability to prolong lifespan
- Fast cure speeds to enhance production efficiencies
- Low energy consumption and no harmful materials to reduce environmental impact and safety concerns
Find out more about UV acrylic PSAs, why you should choose them over existing technologies and how to make a seamless transition based on your current equipment and PSA technology.
Why Choose UV Acrylic PSAs Over Solvent Acrylic PSAs
While solvent acrylic PSAs provide excellent durability, they come at a higher cost compared to UV acrylic PSAs.
- Costly supply: Due to the solvents evaporating during processing, about half of a solvent acrylic PSA’s supply yield is lost*. This means more supply must be purchased to account for what will be lost during production.
UV acrylic PSAs are formulated as 100% solids; so, none of the yield supply will be lost from evaporation; there are no solvents to burn off.
- Slowed Production: Due to the evaporation process, production can be slowed down with solvent acrylic PSAs, especially if application requires multiple adhesion layers to be laminated (and therefore, production passes) to meet a specific coating weight.
UV acrylic PSAs, however, offer fast production speeds, even for thick coat weights; nothing needs to evaporate off, so there is no need to wait or do multiple passes.
- Additional equipment: In order to burn off solvents, a facility must account for drying ovens, thermal oxidizers and ventilation systems to maintain a seamless production and protect workers.
This is not required with UV acrylic PSAs, since they do not contain solvents. This allows for less equipment needs and more facility space for cost effectiveness along with reduced health risks for workers.
- Flammability risks: Since solvent acrylic PSAs contain solvents, which pose a potential risk for fires, additional precautions must take place when storing and shipping to reduce danger likelihood. The storage requirements also limit how much product a plant can keep on site at a given time, which can impact production output and revenue generation.
This is not a concern with UV acrylic PSAs, helping to simplify storage and shipping complexities as well as cost constraints.
What to Expect if Switching from Solvent Acrylic to UV Acrylic PSAs in Your Production
While solvent acrylic and UV acrylic PSAs are based on acrylics, UV acrylic PSAs do not require burning off solvents. Therefore, the equipment you have for solvents cannot work for UVs. Instead, to make the switch, you will need to invest in a hot melt PSA coating line with UV lights. This equipment is designed for PSA technologies that are comprised of 100% solids, which hot melt and UV acrylic PSAs have in common with one another. The hot melt PSA coater will provide the coating capabilities needed for UV acrylic PSAs, and the addition of UV lights will help cure them.
Unlike solvent coating equipment, a hot melt PSA coater does not require drying ovens, thermal oxidizers and ventilation systems to account for solvent or volatile organic compound VOC evaporation.
While you will have the upfront investment, hot melt PSA coaters are less expensive than solvent coating equipment in the long run and can help reduce overall costs by:
- Decreasing energy usage: No longer accounting for solvents burning off can help you reduce energy usage by approximately 85%**. This will also help reduce your monthly energy expenses.
- Increasing production efficiencies: Without the need to evaporate solvents, you will be able to run coat weights five times faster or more, depending on adhesive deposition and number of UV lights**.
- Reducing plant footprint: With the combination of no longer evaporating solvents and running a more streamlined production, your overall carbon footprint will decrease, allowing you to run a more environmentally-friendly operation.
- Simplifying storage complexities: Unlike solvents, UV acrylic PSAs do not require storage that follows EPA regulations to prevent flammability or safety risks, resulting in reduced costs for additional or complex storage methods.
Why Choose UV Acrylic PSAs Over Hot Melt PSAs
While rubber-based hot melt PSAs are 100% solids and less of an environmental impact than solvent acrylic PSAs, there are still limitations to using them:
- Long-Term Oxidative Stability: Rubber polymers in hot melt PSAs have unstable C=C bonds as well as rheological limitations in formulated styrene block copolymer adhesives. This causes the rubber to become brittle and lose adhesion when exposed to UV light.
UV acrylic PSAs do not contain rubber polymers and therefore do not have this issue.
- Strong Shear Levels at High Temperatures: When rubber-based hot melt PSAs are subjected to high heat, their styrene domains lose physical crosslinks that result in oozing problems.
UV acrylic PSAs are formulated differently and offer high temperature performance without losing adhesive performance.
- UV, Plasticizer and Chemical Resistance: Rubber-based hot melt PSAs lack chemical crosslinking and oligomeric additives, limiting their application usage.
UV acrylic PSAs do not possess this limitation, offering design flexibility to address demanding applications.
- Cold Temperature Conditions: Rubber-based hot melt PSAs lose their tack in conditions lower than 10°F
UV acrylic PSAs offer good bonding abilities even at cold temperatures, which increases their application use.
What to Expect if Switching from Rubber-Based Hot Melt PSAs to UV Acrylic PSAs in Your Production
While UV acrylic PSAs and rubber-based hot melt PSAs are based on different chemistries, they require similar equipment, because they are both comprised of 100% solids. Therefore, switching to UV acrylic from rubber-based hot melt will require minimal capital investment. You already have a hot melt PSA coater; you only need to incorporate UV lights with these components:
- Drum unloader
- Buffer tank
- Feed lines
- Slot-die coating head (optional)
However, you can also continue to run rubber-based hot melts and don’t need to stop doing so simply because you want to run UV acrylics. You will need to keep in mind the following:
- You'll need a separate delivery system (drum loader), since UV acrylic PSAs and rubber-based hot melt PSAs have different chemistries.
- These adhesives are sometimes processed at different temperatures. It’s recommended that you have dedicated transfer lines and buffer tanks to avoid mixing.
- If you plan to run UV acrylic and rubber-based hot melt PSAs on the same coating line, separate equipment and special care will be required to avoid cross-contamination of the molten adhesives in your coating equipment, since the two chemistries are not compatible with each other.
Without much of an upfront investment, incorporating UV lights with a hot melt PSA coater will help you:
- Increase application capabilities: By using one coating machine for two PSA technologies that offer different levels of adhesion and durability, you can provide a broad portfolio, including solutions for permanent and removable applications.
- Promote solventless production: Your ability to manufacture products with two PSA technologies that are both comprised of 100% solids will enable brand owners to show end-users they are heightening sustainability features throughout their processes.
- Decrease carbon footprint: By eliminating steps to evaporate solvents and incorporating fast processing speeds, you’ll be able to deliver end-use applications at a faster rate compared to a production involving solvents.
Best Practices for Coating UV Acrylic PSAs
Once you have a hot melt PSA coater with UV lights, you should establish a system within your facility to oversee these new equipment components:
- Supervise UV Lamps: By supervising the UV lamps, you’ll maintain consistent quality of the application being produced. This includes ensuring all clear or reflective surfaces are kept clean.
- Monitor UV Light Intensity: Assessing how UV light intensity and dosage impacts adhesive performance will ensure consistency in product quality. This should be completed in conjunction with adhesive performance testing.
- Develop UV System Maintenance Program: Establishing a system to administer the UV system’s condition will be crucial to keeping production moving efficiently without extra downtime.
How Bostik Can Help You Switch to UV Acrylic PSAs
Bostik’s technical service team is here to support you throughout the process of testing and troubleshooting. We’ll work with you to provide suggestions on customized adhesive formulations for your specific needs. Further, we can help you address issues on-site to ensure you have a seamless transition.
Ready to incorporate UV acrylic PSAs into your manufacturing? Talk to a Bostik expert today about your current processes and what you’ll need to make the switch for a seamless production.
*as on average, solvents are 50% solids
**based on internal testing
Other Relevant Content:
Why Choose UV Over Hot Melts and Solvents for Tapes, Graphics Applications
Address Tape Sustainability Needs Without Sacrificing Performance
©2023 Bostik, Inc. All Rights Reserved
All information contained herein is believed to be accurate as of the date of publication, is provided “as-is” and is subject to change without notice. To review our full U.S. Legal Disclaimer, visit: https://bostik.com/us/en_US/privacy-policy/legal-disclaimer